H07V-U H07V-R H07V-K
- Standard DIN VDE 0281-3, BS 6004, HD 21.3; ASTM, IEC, DIN, BS, AS, CSA, NFC, SS, etc.
Construction
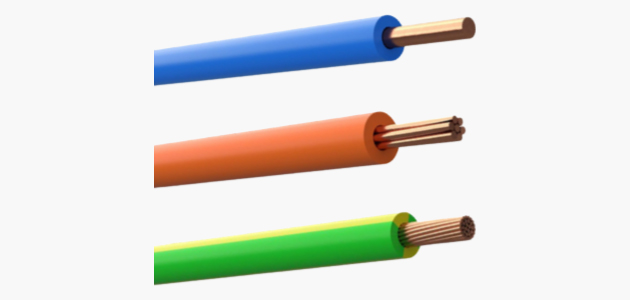
Conductor
class 1 solid -H07V-U
class 2 stranded H07V-R
class 5 flexible H07V-K
Insulation
Color of insulation
Maximum Conductor Operating Temperature
Lowest Ambient Temperature For Fixed Installation
Lowest Installation Temperature
Maximum Short-Crcuit Conductor Temperature
Nominal Voltage
Test Voltage
Flame Retardant
Technical Specifications
Nominal Cross Section Area |
Number of wires /Diameter of wires |
Approx. Diameter of Conductor |
Thickness of Insulation |
Approx. Overall Diameter |
Approx. Weight of cable |
Max. Conductor Resistance at 20°C |
Min. Insulation Resistance at 70°C |
mm2 | No./mm | mm | mm | mm | kg/km | Ω/km | MΩ.km |
1.5 | 1/1.38 | 1.38 | 0.7 | 2.9 | 20.9 | 12.1 | 0.011 |
2.5 | 1/1.78 | 1.78 | 0.8 | 3.5 | 32.8 | 7.41 | 0.010 |
4 | 1/2.25 | 2.25 | 0.8 | 4.0 | 47.9 | 4.61 | 0.0087 |
6 | 1/2.76 | 2.76 | 0.8 | 4.5 | 67.8 | 3.08 | 0.0074 |
10 | 1/3.57 | 3.57 | 1.0 | 5.7 | 112.0 | 1.83 | 0.0072 |
Nominal Cross Section Area |
Number of wires /Diameter of wires |
Approx. Diameter of Conductor |
Thickness of Insulation |
Approx. Overall Diameter |
Approx. Weight of cable |
Max. Conductor Resistance at 20°C | Min. Insulation Resistance at 70°C |
mm² | No./mm | mm | mm | mm | kg/km | Ω/km | MΩ.km |
1.5 | 7/0.52 | 1.56 | 0.7 | 2.96 | 21.5 | 12.1 | 0.010 |
2.5 | 7/0.68 | 2.04 | 0.8 | 3.64 | 34.6 | 7.41 | 0.0099 |
4 | 7/0.85 | 2.55 | 0.8 | 4.15 | 49.5 | 4.61 | 0.0082 |
6 | 7/1.04 | 3.12 | 0.8 | 4.72 | 69.5 | 3.08 | 0.0070 |
10 | 7/1.35 | 4.05 | 1.0 | 6.05 | 116.3 | 1.83 | 0.0067 |
16 | 7/1.70 | 5.10 | 1.0 | 7.10 | 167.1 | 1.15 | 0.0056 |
25 | 7/2.14 | 6.42 | 1.2 | 8.82 | 268.8 | 0.727 | 0.0053 |
35 | 7/2.52 | 7.56 | 1.2 | 9.96 | 364.6 | 0.524 | 0.0046 |
50 | 19/1.78 | 8.90 | 1.4 | 11.7 | 517.7 | 0.387 | 0.0046 |
70 | 19/2.14 | 10.70 | 1.4 | 13.5 | 708.2 | 0.268 | 0.0040 |
95 | 19/2.52 | 12.60 | 1.6 | 15.8 | 959.7 | 0.193 | 0.0039 |
120 | 37/2.03 | 14.21 | 1.6 | 17.41 | 1194.8 | 0.153 | 0.0035 |
150 | 37/2.25 | 15.75 | 1.8 | 19.35 | 1493.4 | 0.124 | 0.0035 |
185 | 37/2.52 | 17.64 | 2.0 | 21.64 | 1843.5 | 0.0991 | 0.0035 |
240 | 61/2.25 | 20.25 | 2.2 | 24.65 | 2383.5 | 0.0754 | 0.0034 |
300 | 61/2.52 | 22.68 | 2.4 | 27.48 | 2971.5 | 0.0601 | 0.0033 |
400 | 61/2.85 | 25.65 | 2.6 | 30.85 | 3927.4 | 0.0470 | 0.0031 |
Nominal Cross Section Area |
Number of wires /Diameter of wires |
Approx. Diameter of Conductor |
Thickness of Insulation |
Approx. Overall Diameter |
Approx. Weight of cable |
Max. Conductor Resistance at 20°C | Min. Insulation Resistance at 70°C |
mm² | No./mm | mm | mm | mm | kg/km | Ω/km | MΩ.km |
1.5 | 30/0.25 | 1.57 | 0.7 | 2.97 | 3.67 | 13.3 | 0.010 |
2.5 | 49/0.25 | 2.02 | 0.8 | 3.62 | 4.42 | 7.98 | 0.0095 |
4 | 56/0.30 | 2.9 | 0.8 | 4.5 | 5.30 | 4.95 | 0.0078 |
6 | 84/0.30 | 3.6 | 0.8 | 5.2 | 6.00 | 3.30 | 0.0068 |
10 | 84/0.40 | 4.7 | 1.0 | 6.7 | 7.70 | 1.91 | 0.0065 |
16 | 126/0.40 | 5.9 | 1.0 | 7.9 | 8.90 | 1.21 | 0.0053 |
25 | 196/0.40 | 7.3 | 1.2 | 9.7 | 10.90 | 0.780 | 0.0050 |
35 | 276/0.40 | 9.2 | 1.2 | 11.6 | 12.80 | 0.554 | 0.0043 |
50 | 396/0.40 | 11 | 1.4 | 13.8 | 15.20 | 0.386 | 0.0042 |
70 | 360/0.50 | 13.1 | 1.4 | 15.9 | 17.30 | 0.272 | 0.0036 |
95 | 475/0.50 | 14.4 | 1.6 | 17.6 | 19.20 | 0.206 | 0.0036 |
120 | 608/0.50 | 16.3 | 1.6 | 19.5 | 21.10 | 0.161 | 0.0032 |
150 | 756/0.50 | 18.7 | 1.8 | 22.3 | 24.10 | 0.129 | 0.0032 |
185 | 925/0.50 | 20.1 | 2.0 | 24.1 | 26.10 | 0.106 | 0.0032 |
240 | 1221/0.50 | 23.1 | 2.2 | 27.5 | 29.70 | 0.0801 | 0.0031 |
Minimum bending radius: | For cable diameter D (mm) | |||
D≤8 | 812 | D>20 |
| |
Normal use | 4 D | 5 D | 6 D | 6 D |
Careful bending at termination | 2 D | 3 D | 4 D | 4 D |
Quality Control
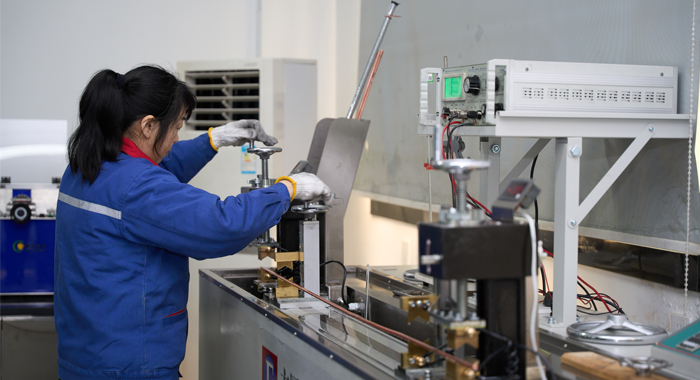
Raw Material Test
NPC has always chosen raw material suppliers who have a good reputation, possess stable supply capabilities and have passed international quality system certifications (such as ISO 9001). And establish a long-term cooperative relationship with it, forming a stable and reliable raw material supply chain.
We will ensure that all raw materials are subject to strict inspection procedures upon entry to the factory, and can only be stored in the warehouse after they have been confirmed to meet the standards.
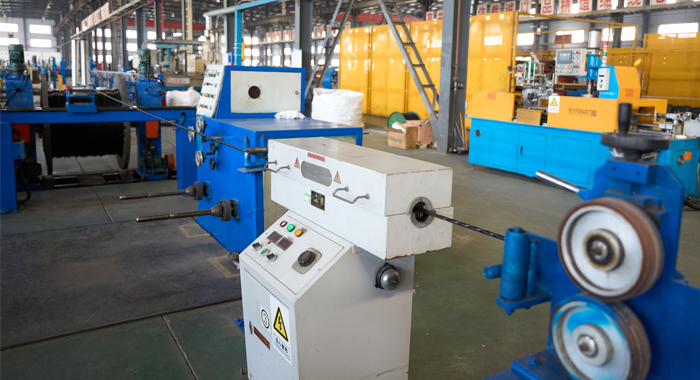
Process inspection
NPC has strict quality control procedures for each process in the cable production process.
Process documents: Develop detailed process flow and operation instructions to clarify the operating specifications and quality standards of each process.
Equipment calibration: Regularly calibrate key equipment such as wire drawing machines, stranding machines, extruders, and diameter gauges to ensure that the accuracy meets the requirements.
First piece confirmation: Before each batch of production, the first piece is trial-produced to confirm that the process parameters, product dimensions, electrical performance, etc. meet the standards before mass production can be carried out.
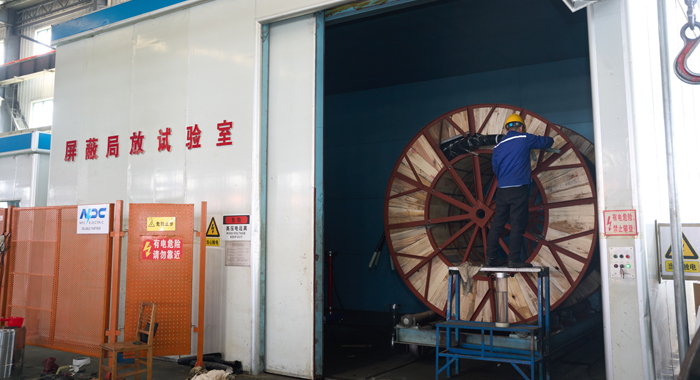
Finished Product
Inspectors conduct ex-factory inspections on cables according to relevant standards and corresponding product inspection specifications to ensure that each ex-factory product complies with the process regulations.
Application
Technical Advantages
Product Packaging
Related Products
FAQ From Customers
-
What are the advantages of power cables and overhead lines?(1) Reliable operation, because it is installed in a hidden place such as underground, it is less damaged by external forces, has less chance of failure, and the power supply is safe, and it will not cause harm to people; (2) The maintenance workload is small and frequent inspections are not required; (3) No need to erect towers; (4) Help improve power factor.
-
Which aspects should be considered when choosing the cross section of a power cable?(1) The long-term allowable working current of the cable; (2) Thermal stability once short circuited; (3) The voltage drop on the line cannot exceed the allowable working range.
-
What are the measures for cable fire prevention?(1) Use flame-retardant cables; (2) Use fireproof cable tray; (3) Use fireproof paint; (4) Fire partition walls and fire baffles are installed at cable tunnels, mezzanine exits, etc.; (5) Overhead cables should avoid oil pipelines and explosion-proof doors, otherwise local pipes or heat insulation and fire prevention measures should be taken.
-
What should be paid attention to during the transportation and handling of cables?(1) During transportation, loading and unloading, cables and cable reels should not be damaged. It is strictly forbidden to push the cable reels directly from the vehicle. Generally, cables should not be transported and stored flat. (2) Before transporting or rolling the cable reel, ensure that the cable reel is firm, the cable is wound tightly, the oil pipe between the oil-filled cable and the pressure oil tank should be fixed without damage, the pressure oil tank should be firm, and the pressure indication should meet the requirements.
-
What inspections should be carried out for the acceptance of cable lines?(1) The cable specifications should meet the regulations, the arrangement should be neat, no damage, and the signs should be complete, correct and clear; (2) The fixed bending radius of the cable, the related distance and the wiring of the metal sheath of the single-core power cable should meet the requirements; (3) The cable terminal and the middle head should not leak oil, and the installation should be firm. The oil pressure of the oil-filled cable and the meter setting should meet the requirements; (4) Good grounding; (5) The color of the cable terminal is correct, and the metal parts such as the bracket are completely painted; (6) There should be no debris in the cable trench, tunnel, and bridge, and the cover should be complete.